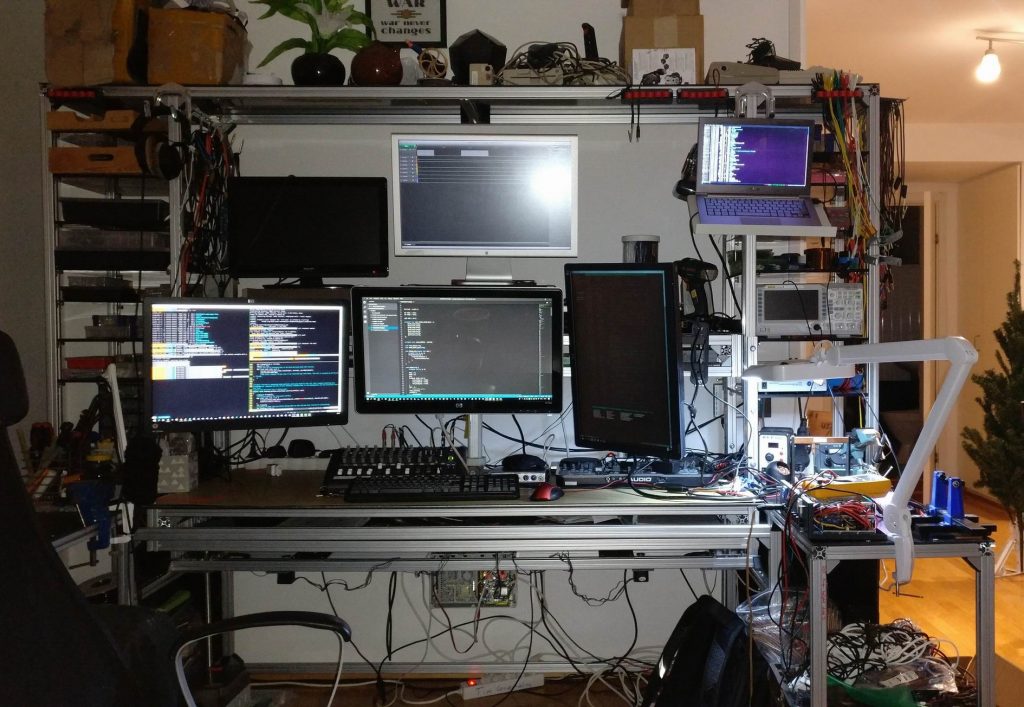
So I have wanted to build a desk for many years now, ideas have grown and so has the big feature list. But since my interest have moved away from software to electronics my requirements have changed. I need a lot bigger work space for tools and more shelves for instruments, and still a lot of screens.
So 3 years ago I started on my desk design. I decided that I wanted to go for aluminium profiles for my frame, both because it’s flexible and something I had not tried it before.
I also wanted as much of the construction to be as precise as possible, so everything is constructed in CAD. Mechanics strength tested, mechatronics is movement tested, material purchase planned and material is CNC cut as much as possible.
By the end of 2018 I started the weeks long process of assemble it all.
I made a drawing with assembly instructions based on my CAD design Skrivbord (Workstation, Gremalm).pdf. But I quickly decided to change the assembly order to make two stable outer pieces to build the rest on, it also meant that I didn’t have to turn the whole assembly too much.
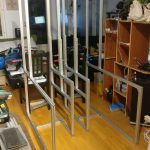
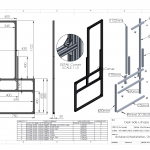
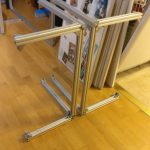
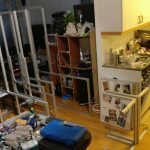
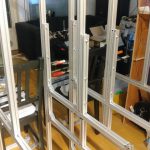
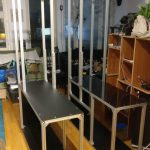
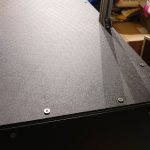
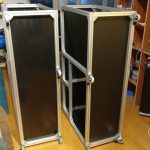
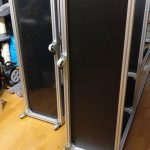
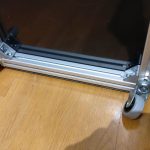
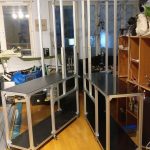
The two outer pieces assembled.
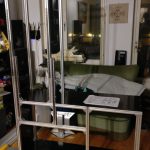
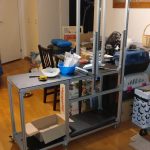
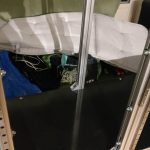
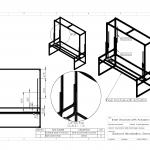
Sliders for the raise-able desk and shelf are mounted on the sides. It’s MGN12H linear sliders often used in smaller CNC builds.
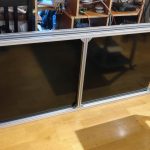
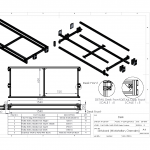
Desk assembled.
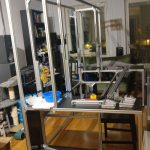
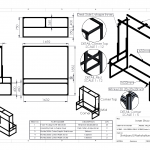
Center pieces to hold the two sides together.
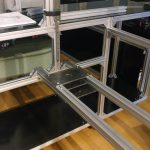
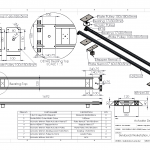
To make the desk move up and down in the sliders I’ve constructed a linear actuator using a threaded rod, some pulleys and a stepper motor. It all goes together in this lower center assembly.
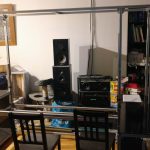
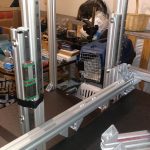
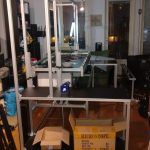
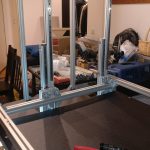
The desk was lifted in place and screwed into the MGN12H blocks. It should have been a lot of over constrains in the desk assembly, but it could move up and down pretty easy.
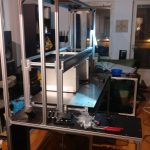
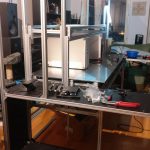
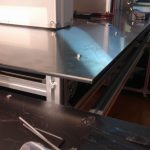
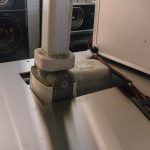
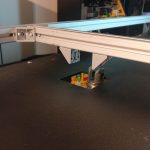
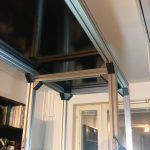
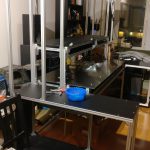
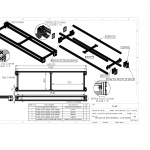
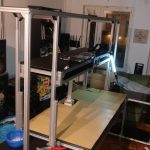
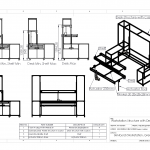
The desk shelf will hold all the monitors, and is attached to the big desk. That means when the desk is raised or lowered the computer monitors will follow. I used an old used actuator for this purpose that I had laying around.
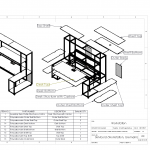
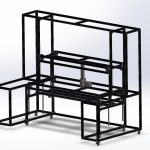
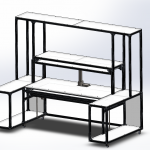
Instead of using CNC cut polycarbonate I ordered laser cut ABS sheets for the desk because it was a lot cheaper. I found this neat laser cut order system where I could upload my DXF-files directly on the web and isntantly get a quote. https://smidyo.com/
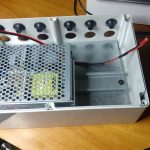
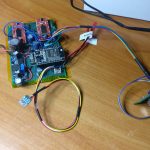
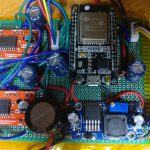
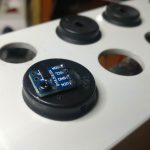
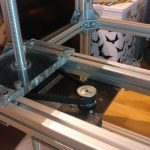
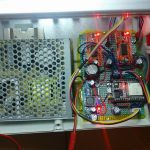
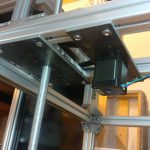
To raise and lower the desk I made a small control box. It have two stepper drivers inside that drives each side of the desk.
A VL53L0X ToF (Time-of-Flight) sensor is measuring the distance to the desk so the control box can regulate the height. This also gives me an absolute height of the desk when restarting the MCU.
An ESP32 connects to a MQTT server and serves a desired height topic, when a new goal is set the control box will start to raise/lower the desk until the goal is set.
https://github.com/TimGremalm/SkrivbordDeskStepper
There’s also manual override for the desk with ordinary switches.
So in the end, was it worth it? No; the whole construction ended up far too expensive both in cost and time. But it was a nice experience to design something this big and follow through building it.
A far more effective workstation would be to purchase a cheap Ikea shelf and then place a raisable desk in front of it.